Brief introduction of production line
The production process for these sandwich panels involves a continuous spray foaming of polyurethane between two surface plates, with the materials moving forward uniformly on a conveyor belt. During thisprocess,polymerization occurs, leading to the solidification of the materials.Subsequently, the sandwich panels are cut to the desired lengths following
uninterrupted roll forming.The output of this production line, namely PIR/PUR sandwich panels, represents a highly regarded building material for walls and roofs. These panels offer exceptional properties such as superior thermal insulation,soundproofing, fire resistance, waterproofing, portability, and environmental
friendliness. They find versatile applications in enhancing the external walls of tall buildings and prestigious office structures.
PRONTO TECHNOLOGY EDGE
Decoiler :
The metal coil will be open into sheet and fed into roll forming machine by this part .
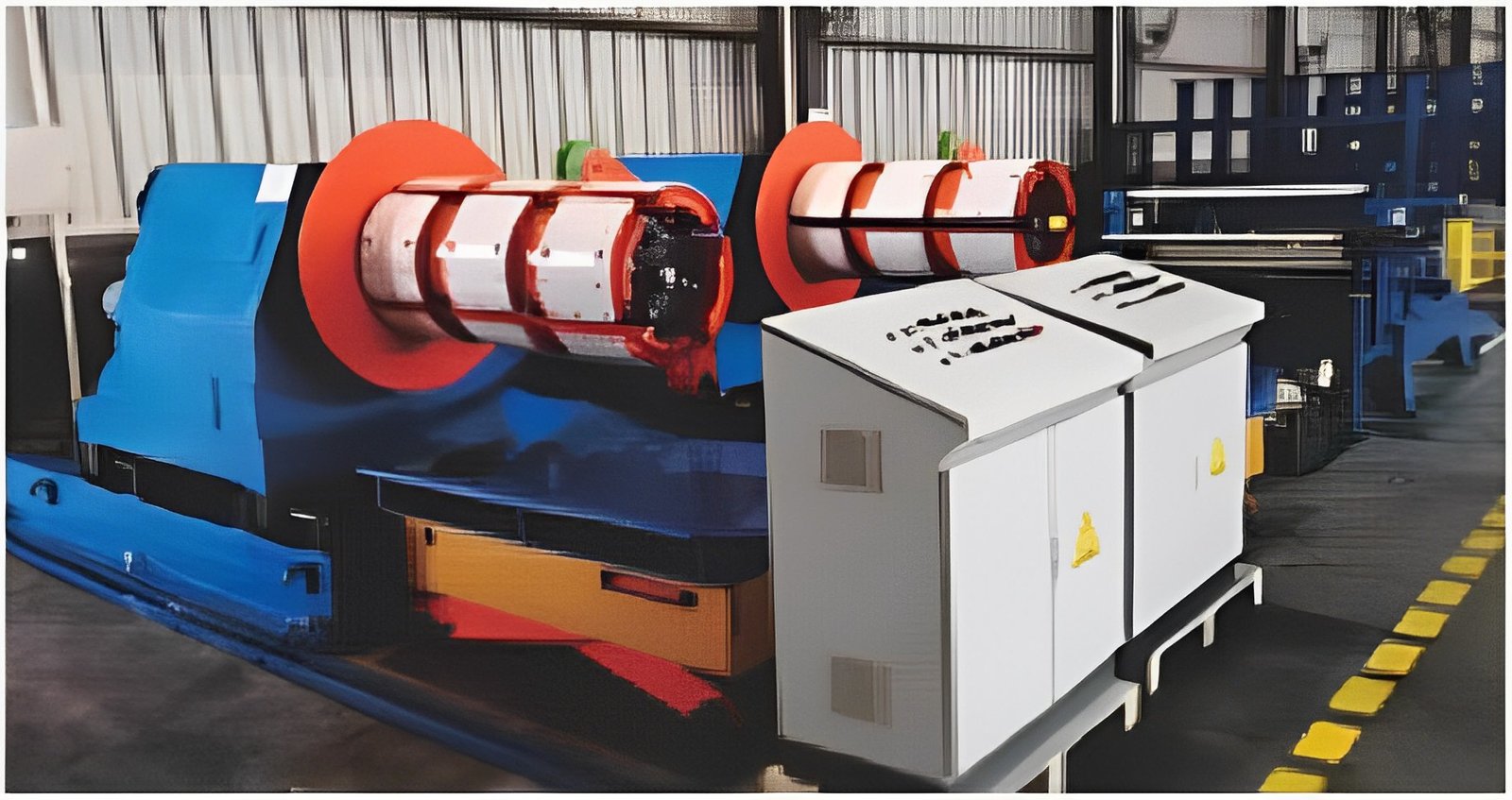
SPECIFICATION:
- 1) Capacity: max. 5tons
- 2) Uncoiling speed : 0-30m/min(adjustable)
- 3) Width of material: max. 1250mm
- 4) Adjusting Center : max. 250mm
- 5) Max. Hydraulic pressure :16Mpa
- 6) Motor power of hydraulic motor:3KW
- 7) Air pressure:0.7Mpa
Shearing device and protective film covering
- 1. Thickness 0.3~0.8mm
- 2. Cut steel sheet from length to stop the
production , save material . - 3. Cover protective film the surface of the
metal sheet during roll forming process.
During the storage of the final sandwich
panels, the film can protect the final
sandwich panels from dust, so that when
they are used for construction, it’s surface
is beautiful and clean
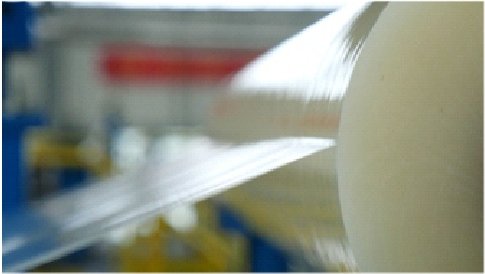
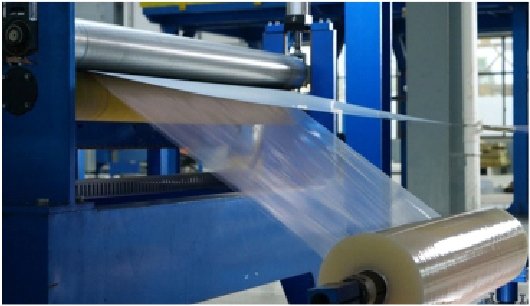
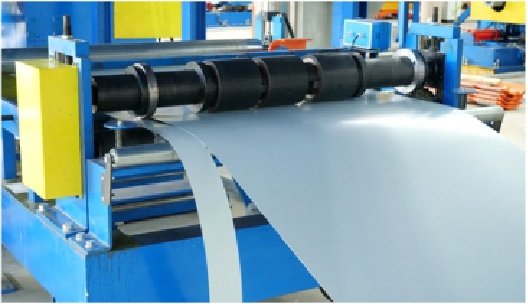
Roll Forming System
In this stage the metal sheet are roll formed
into different panel shapes according to the
panel profile drawing. Several shapes and
designs are possible with these roll forming
stations.
Main specification | |
Machine base structure | 350H steel welded |
Machine architecture | Middle plate- 20mm thick |
Drive mode | Chain drive |
Roller station numbers | 21 stations |
Rollers material |
45# steel, Surface hard chromium plating |
Shaft diameters |
Φ 80mm(solid and thick ) NOT 70mm hollow |
Shaft material |
45# steel, heated and quenched cylindrical grinding, |
Forming speed | 2~12m per minute |
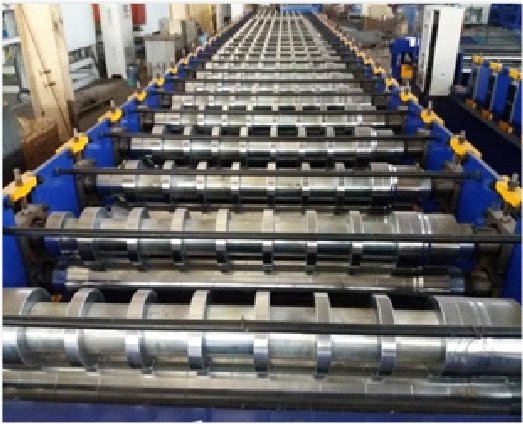
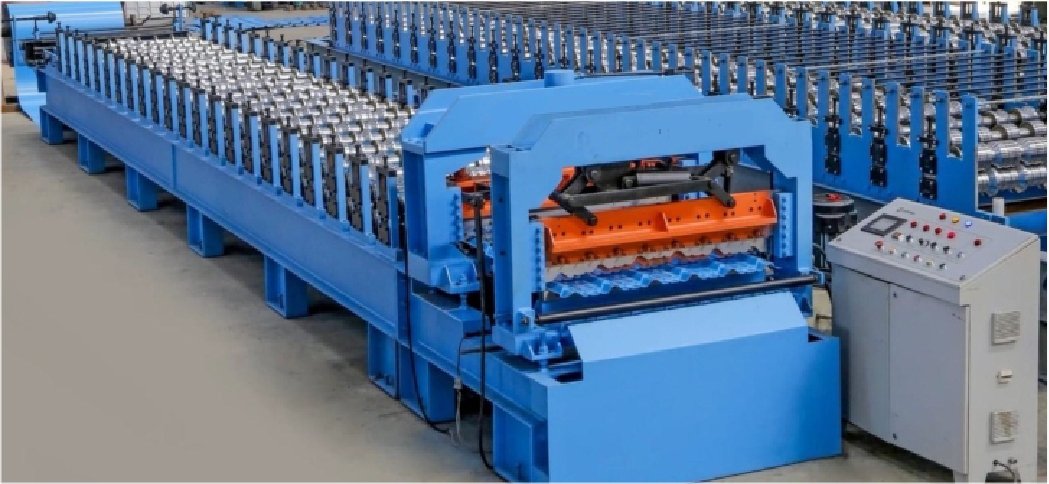
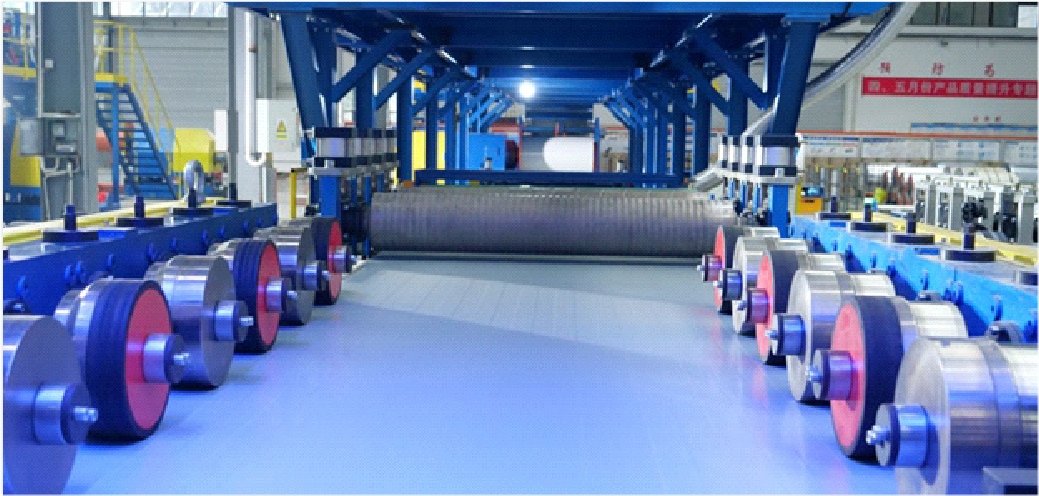
Several shapes and designs are possible with these roll forming stations.
PRODUCT 1: ROOF PANEL
- 1. Input Coil width : 1220mm
- 2. Final width : 1000m
- 3. Metal material: PPGI 0.3~0.8mm or Paper,
plastic or aluminum films. - 4.0 Thickness (rib excluded) : 10~100mm
- 5. Length : max. 12m
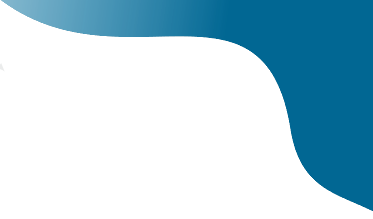

PRODUCT 2: ROOF PANEL
- 1. Input Coil width : 1070mm
- 2. Final width : 1000m
- 3. Metal material : PPGI 0.3~0.8mm or Paper, plasc or aluminum films.
- 4.0 Thickness (rib excluded) : 10~100mm
- 5. Length : max. 12m

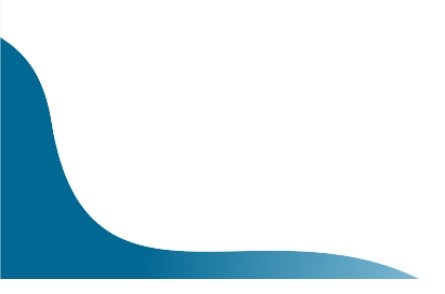
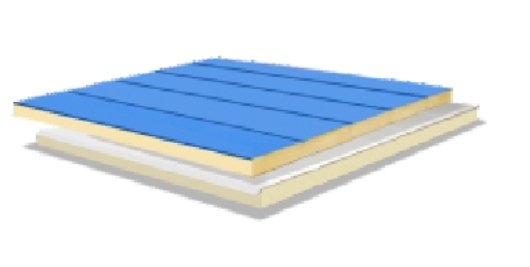
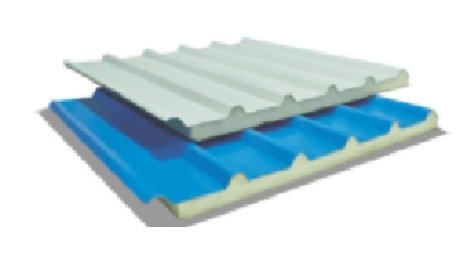
Conveyor system
Long Transit roller path aer upper roll forming machine
Transit path is used to meet double-station down roll forming machines changing profiles without interference, and achieve the transition bridge between up roll forming machine and pre-heating furnace.
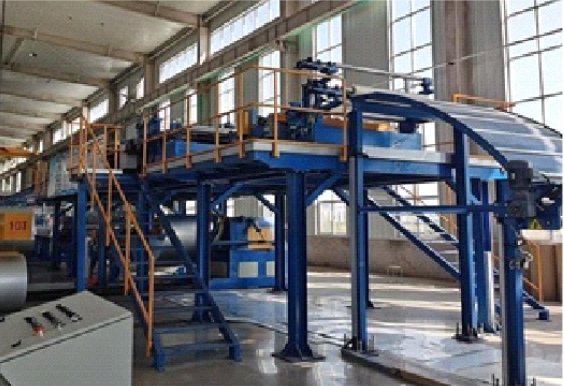
Working plaorm for upper roll forming machines
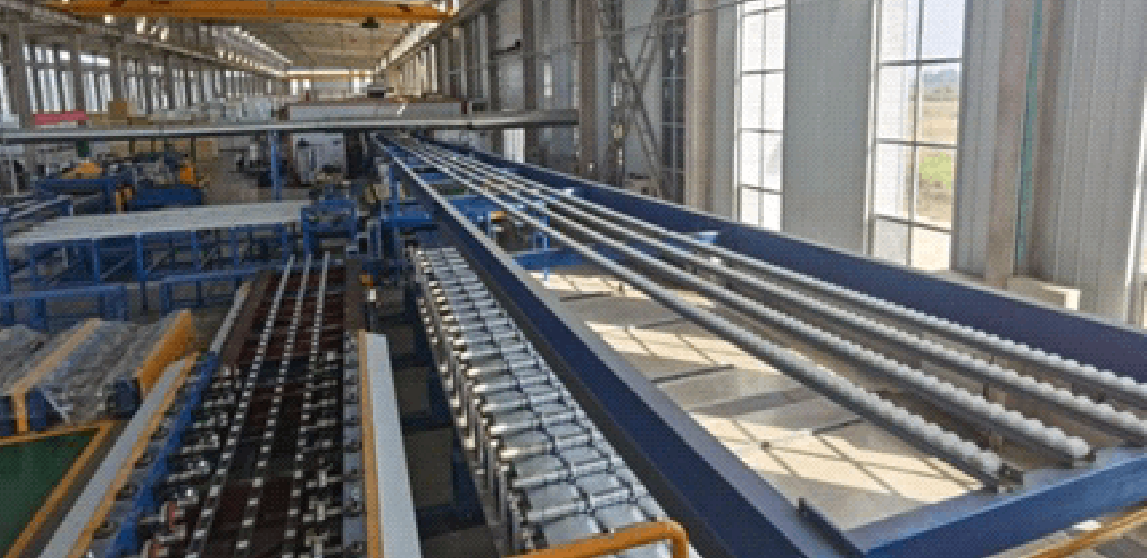
Pre-Heating System
Individually controlled top and bottom steel pre-heaters heat the steel to the correct temperature prior application of the polyurethane. The section includes electrical heating with automatic control to heating upOo 70 C max. Which meet the temperature of PU or PIR production .
Data :
1. Sheet width: Max.1200Mm
2. Guide roller adjust stroke: 100mm
3. Heating power: 36kw
4. Temperature difference: ≤+/-3 ℃
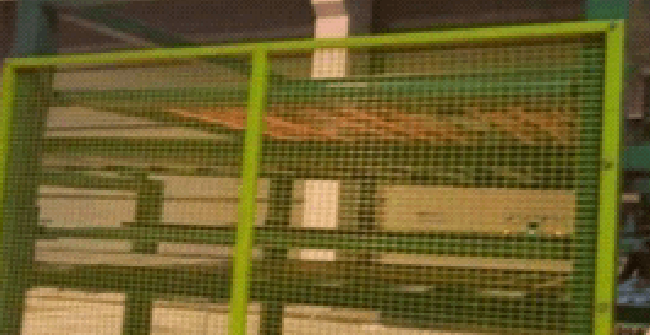
Four Components High Pressure PU Foaming System
Blowing agent and Catalyst mixed real-time in Polyol
With both mobile injection and fix injection
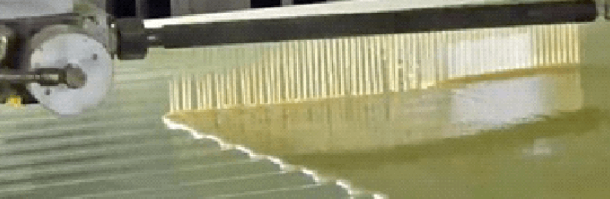
Mobile injection
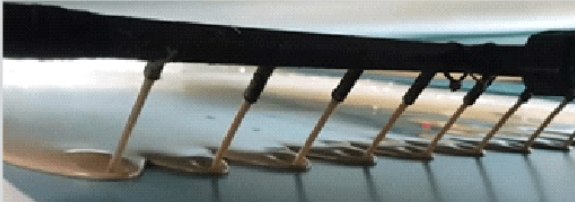
Fix injection
Components high pressure PU foaming system is for 4-components raw material :
Polyol and Isocyanate along with Catlyst and Blowing agent. Each component was measured separately, by PLC , Converters and German precision flowmeter for dual closed-loop control. The dynamic response is very good .It can instantly change the output flow and mixing ratio. The system works by continuous on-line high-pressure mixing. Polyol and Isocyanate are mixed by high-pressure mixing head, the boom is ejected
Friendly interface control, dynamic display the working status and process parameters, and can be set at any time and to modify the parameters; electronic control systems and production lines linked electronically controlled,traffic flow and the proportion of each component adjusted with the speed of double-belt machine, ensure the quality and stability of composite panels to achieve automatic production.
Main Technical data:
1. Output: Mdi: 240-1200kg/h
2. Polyol:200-1000kg/h
3. Core density 30-45kg/m3
4. Working Pressure:100-150 bar
5. Metering pump
6. Metering pump motor: 2*5.5kw
7. Stirring motor: 2*0.75kw
8. Auxiliary equipment
9. Upper Metal Plates Transition Roller
10. Roller Length: 6000 mm
11. Conveyed work pieces’ width: 1200 mm
12. Roller diameter: 70 mm
13. Lower Metal Plates Transition Roller
14. Roller Length: 6000 mm
15. Conveyed work pieces’ width:1200 mm
16. Conveyed work pieces’ height:1200 mm
17. Roller diameter: 70 mm
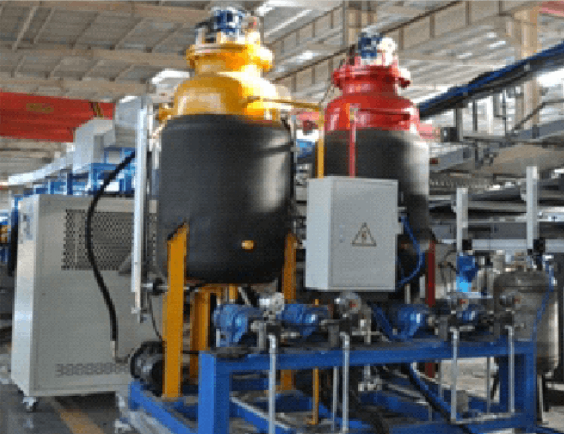
Double Belt Conveyor
Main double belt main press machine
1. When make wall panel , use side molds only .
2. When make roof panel , use both side molds
and boom molds
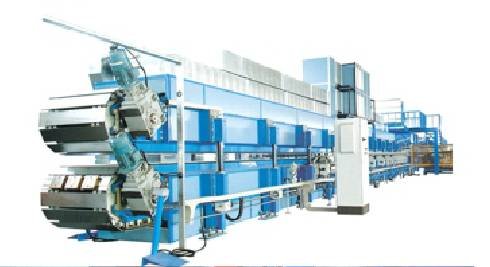
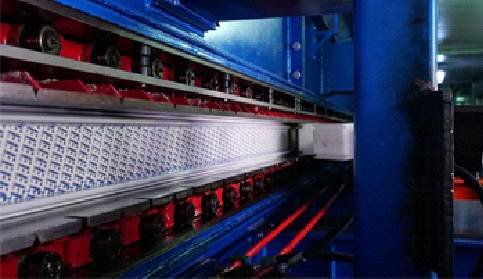

DBL (double belt main press machine ) is the main machine for PU/PIR foaming and forming into solid foam. It decides panel thickness and production speed. It consists of upper and lower steel belt, left and right side belt, molds and transmission system.
The DBL consists of two heavy duty independent conveyor structures (lower and upper) supported by columns which are placed on the floor. The surface of DBL is covered a group of polished steel panels of 200mm chain plates, these panels is connected with wearable bears so that to form a chain driven system with high strength. For these panels, we adopt anti- corrosion welding structure and tooled on high accurate lathe so that to ensure that user can change the panels in future. And for work-piece we adopt double surface seaming and double side in time to keep the level sliding surface smooth ,high precise and hard to deform.
Lower belt is installed a roof panel molds that is anti high temperature and anti corrosion, and also installed Pin shaft on the molds for easy installation and disassembling.
|
DBL upper and lower belt structure
The upper and lower DBL is driven by gear box controlled by motor and inverter; the speed can be adjusted in order to keep the same phase. The position of lower DBL is fixed and the height of upper DBL can be adjusted through adjusting the electrical controlling hydraulic jack so that it is very convenient to adjust the different height to suit for different panel thickness. This adjusting technique already applied for the country patent.
Check high finish accuracy of Double belt plate which determines quality of panels manufactured:
Side belt structure
There are two sides DBL at the two sides of upper and lower DBL which can be kept with the same running speed. The distance of two sides DBL can be adjusted through invert-er motor to suit for different sandwich panel width. The adjustment is high precision, convenient operation and high automation.
On the surface of side DBL, there’s a group of mold for roof panels. Mold size is different according to different profile. Position and molds of side belt decides width of panel and keep it certain to avoid insulated material leak-out.Different panel thickness and different panel profile request different molds. The mold material adopt high molecular weight polyethylene(UHMWPE)which is anti-high temperature and anti-corrupt. It is mounted with screw. It is easy to be equipped and disassembled, and longer lifetime .
Feet height of side belt is adjustable; adjust the height of side belt according to height of DBL and ground level to suit production requirement.
Technical data:
- 1. Motor power:2x3KW
- 2. Adjustment motor: 4*1.5kw
- 3. Material of side module:High molecular weight polyethylene(UHMWPE)
- 4. Adjust method of side module: electric motion adjust , auto
- 5. Chain section distance of side module:20mm.
Band Saw Cutting Machine
With speed tracking device
- 1. Cutting length: 2 m (variable according to production speed)
- 2. panel thickness: max. 150 mm
- 3. Cutting distance: max.1600 mm
- 4. Work height: 1200mm
- 5. Band saw motor power: 5Kw
- 6. Power of band saw machine running: 2kw kw
- 7. Conveyor motor: 5 kw
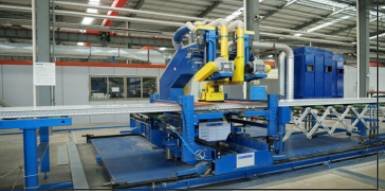
Automatic Panel Cooling system :
With speed tracking device
It consists of main structure in carpentry with high thickness profiles and worked with milling machine. Conveyor chains , wheels , pins and plates. Guides in steel with induction hardening .
Pulley at idle side with hydraulic tension system .
- 1. Motor power of roller table before the cooling conveyor belt: 75 kwX4
- 2. Motor power of roller table after cooling conveyor belt: 5 kwX2
- 3. Roller conveyor speed: 60 m/min (with frequency conversion speed regulation)
- 4. Cooling conveyor belt: length: 12000*15380mm
- 5. The maximum number of panel conveyed by the cooling conveyor belt: 4. pieces (when the production line is working normally)
- 6. Cooling conveyor belt conveying motor power: 5 kwX2
- 7. Maximum cooling panel thickness: 200mm
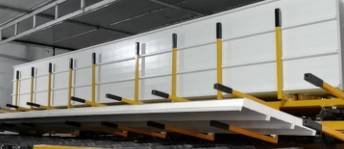
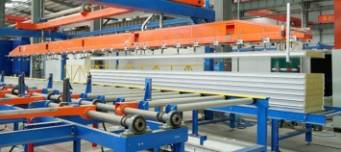
Automatic Panel Packing System
WORKING PROCESS
feed panel—film winding— feeding roller send out panel
- 1. Transmission motor: 2kw
- 2. Film thickness: 25-30 um
- 3. Film width: 500mm
- 4. Packing speed: 0-5m/min (adjustable)
- 5. Roller width:1250mm
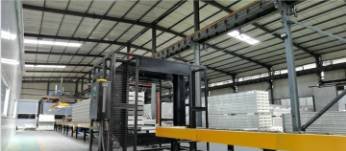
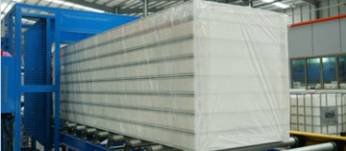